HOW TO REALIZE A ROLLING MILL PLANT DURING A PANDEMIC
A complete rolling mill plant during a worldwide pandemic
AMB has realized, delivered and commissioned a complete rolling mill for special steels in Pakistan, despite all the problems related to covid-19.
Our engineering has upgraded the existing rolling mill from the old production of 35,000MT/y to a final production of 150,000MT/y.
The commission includes the engineering, installation and commissioning of finishing mill, cooling bed, material handing and package accessories, descaling system and others mentioned in scope of work keeping the existing roughing mill and reheating furnace mostly in its current state, and it also incorporates automation mechanism.
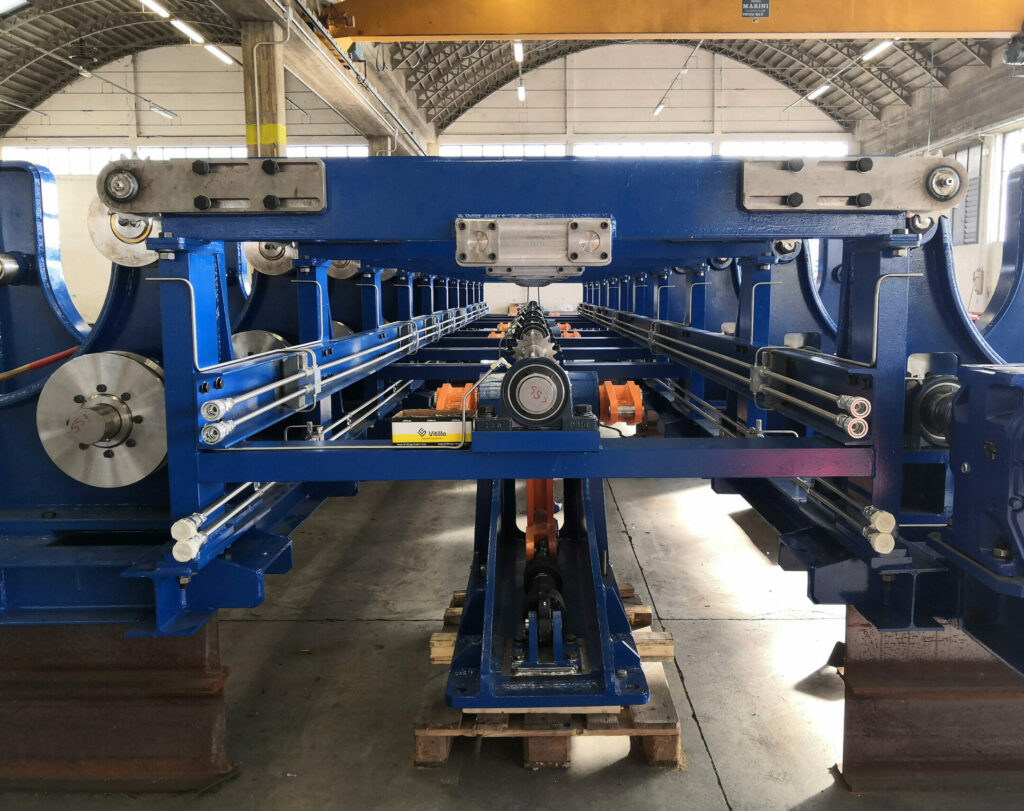
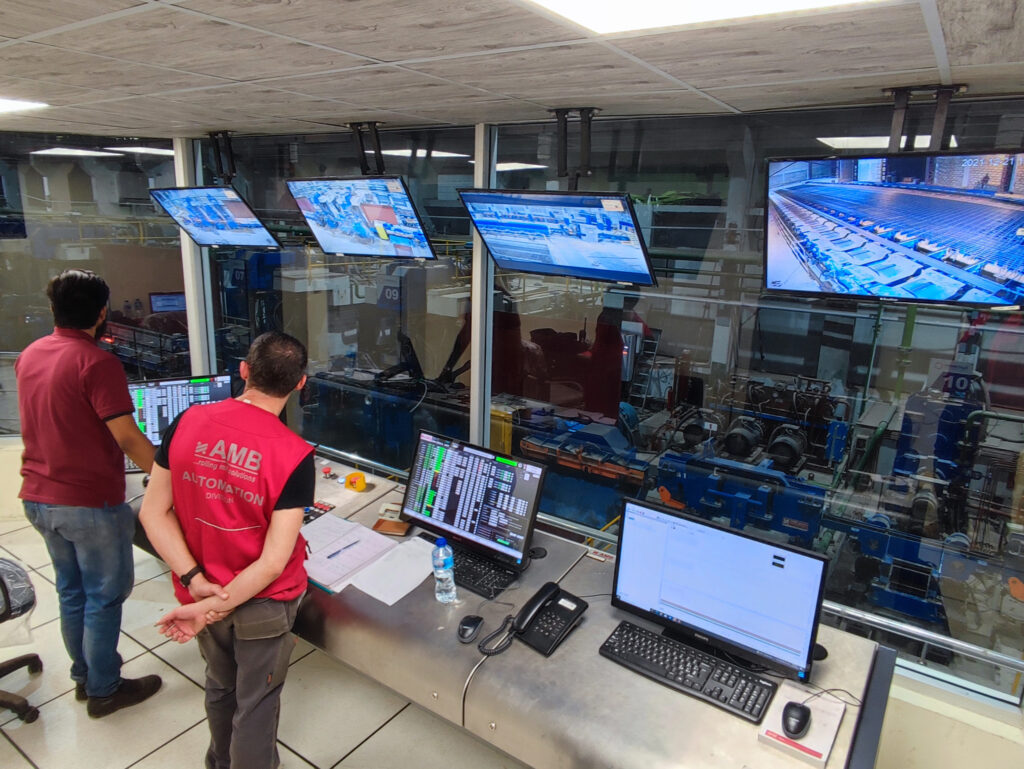
Rolling mill is designed including all modern technological concepts to grant
All this joint to an efficient programming permits a significant reduction in processing costs
High quality of the final product
Efficiency
Economical operation
Flexibility
The proposed plant layout has been studied to give a rational disposition to all components of the plant, so as to facilitate any operation to be carried out.
The various technological and auxiliary areas of the plant are arranged keeping in due consideration material flow and process concepts, requirements of raw material feeding and storage/delivery of the finished products.
REHEATING FURNACE
STANDS
SHEARS
COOLING BED
FINAL CUT AREA
PACKING
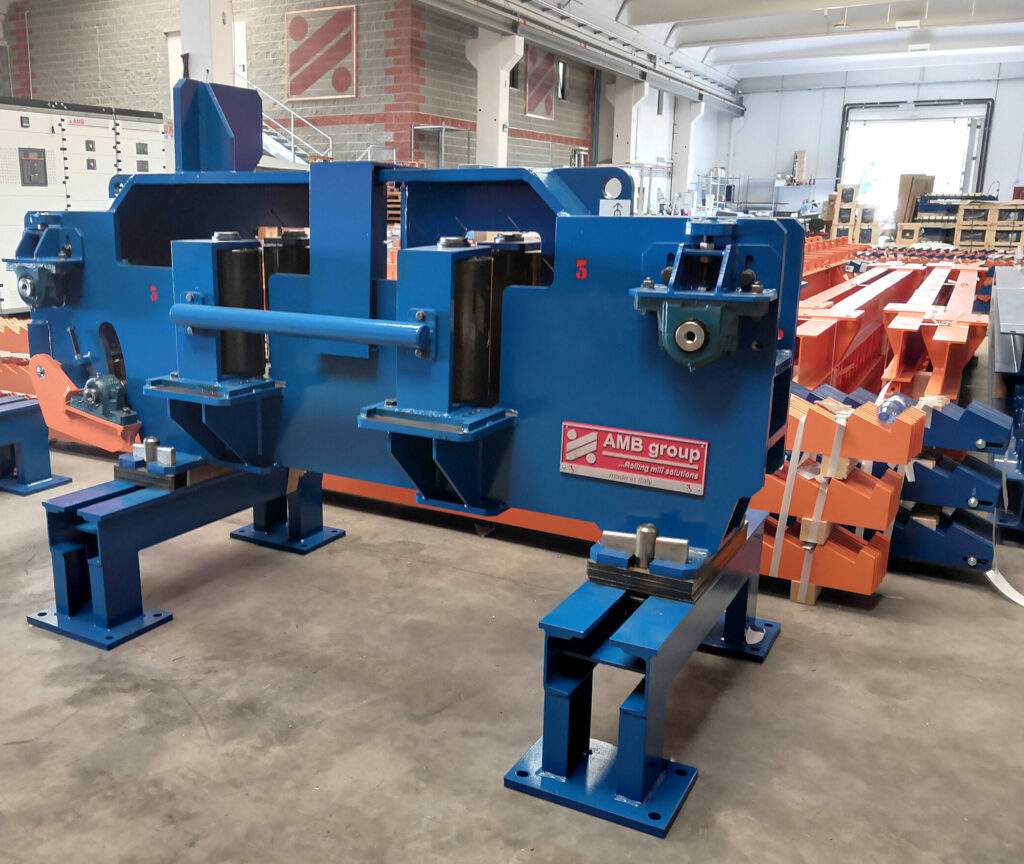
The project is not finished
In fact, all these data refer to the first phase of the project that took place in 2020.
The second phase has begun in 2022 and it previews to increase more the ability to the system.